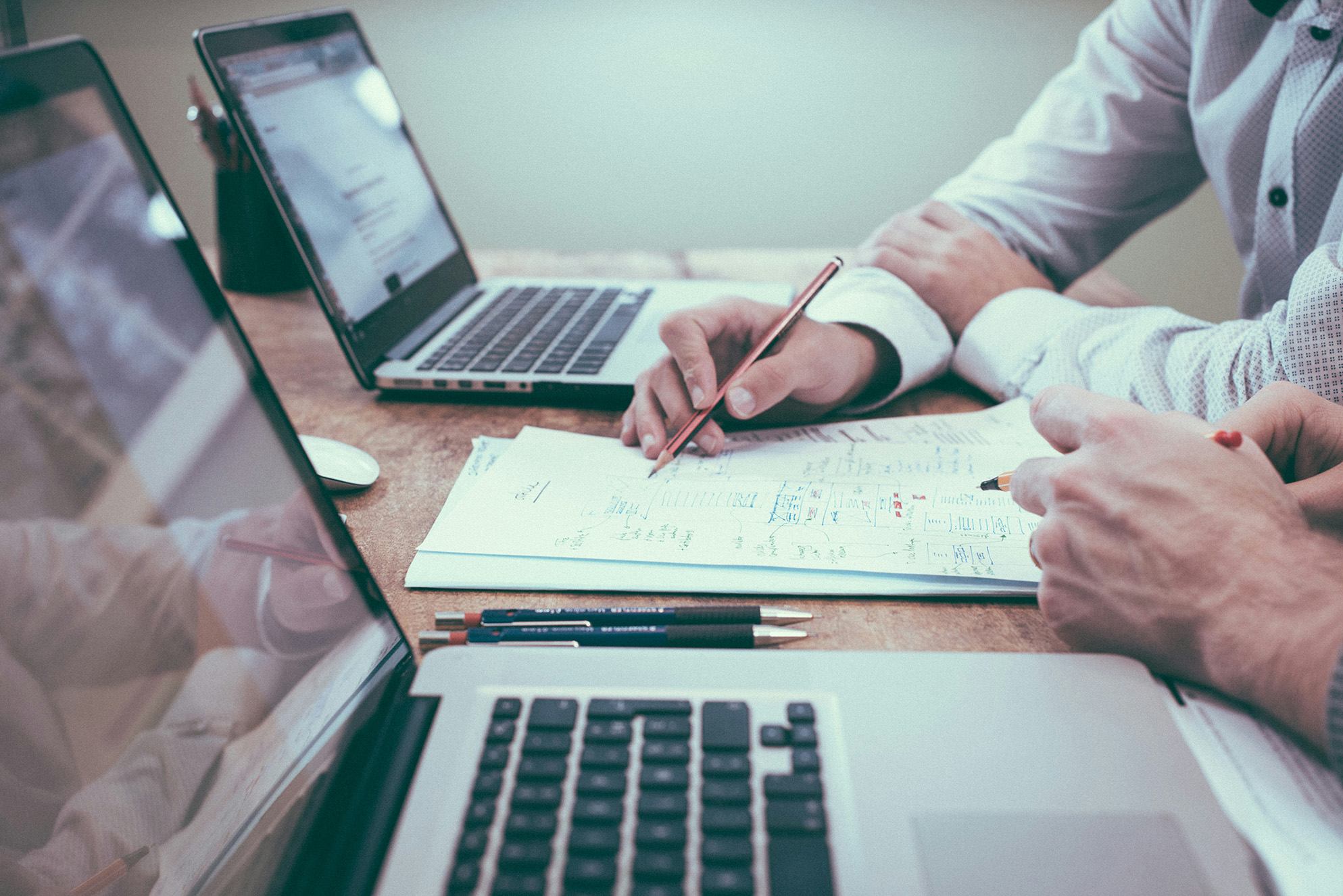
Modernization of Micro850® and Micro870® Control Systems
The Micro850® and Micro870® control systems have undergone a major modernization. The number of inputs/outputs, dimensions, and appearance remain the same. However, new features include project encryption and communication extension with the DF1 protocol. The Micro870® version also adds support for the DNP3 protocol. The upload and download speed of projects has increased by up to 40% compared to previous versions. The most important innovation is improved EtherNet/IP Class 1 communication. To configure all the new functions, the latest version of Connected Components Workbench v.21 must be installed.
Support for the DF1 communication protocol was already available in previous models, but now it's expanded to include DF1 half-duplex master, DF1 half-duplex slave, and DF1 radio modem modes. Through the serial port, it's now possible to set one-way communication (half-duplex), for example, if the main unit does not allow mutual communication, as was the case with the previously used full-duplex mode.
The DNP3 protocol could already be found in the MicroLogixTM 1400 controller, and now it is also included in the new version of the Micro870® control system. Compared to standard RTU protocols such as Modbus, DNP3 is more complex and allows, for example, automatic event logging during communication failures. This protocol can be operated not only via serial link but also over Ethernet.
As already mentioned, a key milestone is the ability to communicate via EtherNet/IP Class 1. This allows us to connect up to 8 devices through network components using standard RJ-45 cables and control them using the implicit messaging method. Unlike explicit messaging, which is based on a request/response model, implicit messaging enables reaction within milliseconds as it works on the principle of I/O data transfer, eliminating the need to wait for a response. In addition to Kinetix 5100 servo drives and PowerFlex 52x frequency inverters, it is now possible to connect remote inputs and outputs using Point I/O modules (product line 1734), significantly expanding not only the total number of I/Os but also the range of applications in which the control system can be deployed for industrial automation.
The Micro850® is available in both older and newer versions with 24 or 48 inputs/outputs and requires a 24 V DC or 110/220 V AC power supply. For outputs, you can choose between source/sink 24 V DC or a variant with relay outputs. The Micro870® offers the same power options but lacks the option to choose the sink transistor type for outputs, and it is available only with 24 inputs/outputs. However, this number can be expanded up to 304 through the use of up to 8 expansion modules. The Micro850® controller can only be expanded to a total of 192 I/Os (4 expansion modules).
You will find the new devices in the catalog under the abbreviation 2080-Lx0E. The Micro850® is labeled as L50E, and the Micro870® as L70E. The letter E stands for Ethernet, indicating at a glance that the controller supports this function. The complete meaning of the catalog number can be found in the image below.